Andy Fordham is a visual effects artist based in Essex, UK. His studio, East Effects, specialises in the design and creation of bespoke props, costumes, and characters for the entertainment industry. Maybe you’ve seen Andy’s work on screen before – his clients include the BBC, 20th Century Fox, Netflix, Sky, and lots of other household entertainment names.
Andy’s creations range from small hand props to large-scale set pieces. 3D printing is a vital tool for his work, and E3D components help make it happen. He uses a Modix BIG-60 and a Creality CR-10 S5, each fitted with Titan Extruders and Volcano HotEnds. He explains:
“E3D products are great to use because they’re reliable and they work well. Each product is competitively priced and easy to order online, and products are thoughtfully designed and well-made. I'm impressed with the clear, published specifications and instructions which make them easy to install and use. This transparency makes E3D stand out against their competitors.”
Let’s look at some of Andy’s work in detail…
Stone-effect statues

These realistic stone-effect statues were commissioned by a pharmaceutical company for display at trade shows and product launches. Each statue was 3D printed in sections on Andy’s Modix BIG-60, before being textured and painted to give a realistic stone effect. Andy explains:
“3D printing with a Titan Extruder and Volcano HotEnd allow me to use bigger nozzle sizes while maintaining print speed. This means I can print large scale objects with better efficiency. Besides improving print times, this wider extrusion of plastic increases the durability of the pieces I make.”

Each statue was printed in sections using a Modix BIG-60 3D printer. E3D’s partnership with Modix means their printers include E3D extrusion systems as standard

What are the advantages of 3D printing here? Working with real stone is an expensive, labour-intensive process. Stone is heavy, so it’s expensive to ship – and there’s always a risk of it being damaged during transit, which is difficult to repair. A 3D printed statue is considerably more lightweight, and after some post processing, it's indistinguishable from the real thing.
3D printing simplifies the prop making process, too. Using traditional prop making methods, a stone-effect statue would first need to be sculpted in clay to create a mould. The mould would then be used to reproduce the form of the statue in a material like fibreglass. 3D printing each statue eliminates the mould-making step, avoiding the use of large amounts of hazardous, expensive silicone and fibreglass material.
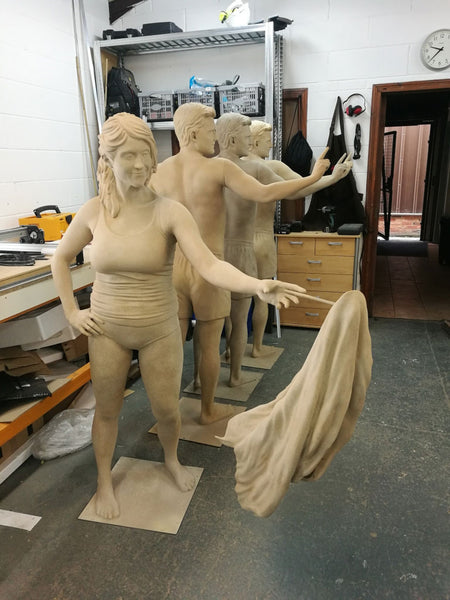
Making a set of statues with traditional methods would use a lot of clay, silicone, and fibreglass. 3D printing removes all this
‘The Monstrous Heart’ life-size brown bear

This life-size brown bear was made for a play at the Traverse Theatre in Edinburgh.
The prop didn’t need to move, but visual realism is still an important factor. Instead of stuffing a real brown bear (which would be awful), Andy 3D printed one.

The bear was digitally sculpted in ZBrush. Andy could then coordinate with the set designer to explore its position before committing to a final pose. The prop was then 3D printed in sections, assembled, furred, and artworked.

Andy’s digital design meant the set designer could choose the bear’s pose before 3D printing

Colour codes represent the various sections the bear was split into in order to 3D print
Hans Moleman!
3D printing was instrumental in creating this scarily realistic articulated puppet of Hans Moleman from ‘The Simpsons’. Andy 3D printed the internal skeleton of the puppet, and 3D printed moulds were used to create lifelike silicone skin to wrap around it.

“It’s like kissing a peanut!” Hans Moleman is 3D printed with silicone skin formed using 3D printed moulds (the puppet, that is…)

The puppet was sculped in ZBrush, and then the mould cores and mechanics were designed

“Oh, no. My brains.” The mechanical inner workings of the puppet are entirely 3D printed

The skin is made of silicone formed using 3D printed moulds. Extra detail was achieved by adding texturing plaster to the mould cores before casting in silicone. ("P-p-please h-hurry...")

Each 3D printed mould has a core and a cavity that’s filled with silicone to create realistic looking skin

“My name is Hans. Drinking has ruined my life. I’m 31 years oollld...”
Thousands of 3D printing applications
Andy’s work shows 3D printing can be used for much more than toys and trinkets: a 3D printer is an indispensable tool in any visual effects workshop. It doesn’t stop there – thousands of 3D printing applications for all kinds of industries are still waiting to be discovered.
“E3D’s passion is clear, and I think they’re pushing boundaries in the field. I’m pleased to be able to support a UK business which has grown from start-up.”
– Andy Fordham, East Effects
You can follow Andy’s work on Instagram.
We’re here for all your 3D printing needs
Do you have 3D printing questions? We have all the knowledge, experience, and parts you need to get maximum 3D print performance for your business. Visit our online shop and find out what we can do for you.
SHOP NOW
Have E3D products helped your business in some way? Get in touch with us and get featured in a case study like this!